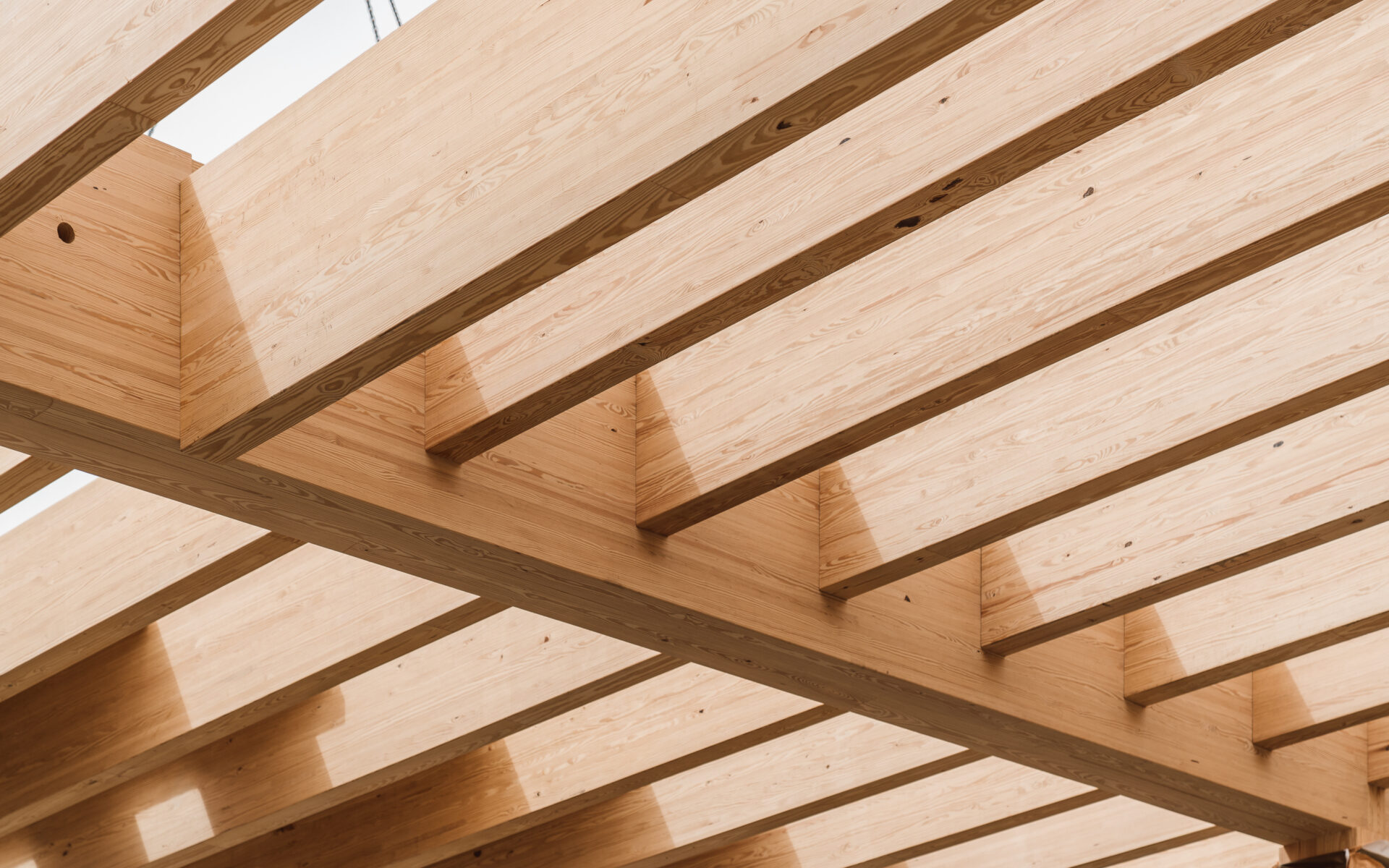
Products
Glued-laminated Timber (Glulam)
An engineered alternative to traditional concrete and steel, glued-laminated timber (glulam) enables the construction of taller, larger, and more structurally efficient timber buildings. Offering superior strength, versatility, and sustainability, glulam is ideal for modern mass timber projects that require both architectural flexibility and high-performance materials.
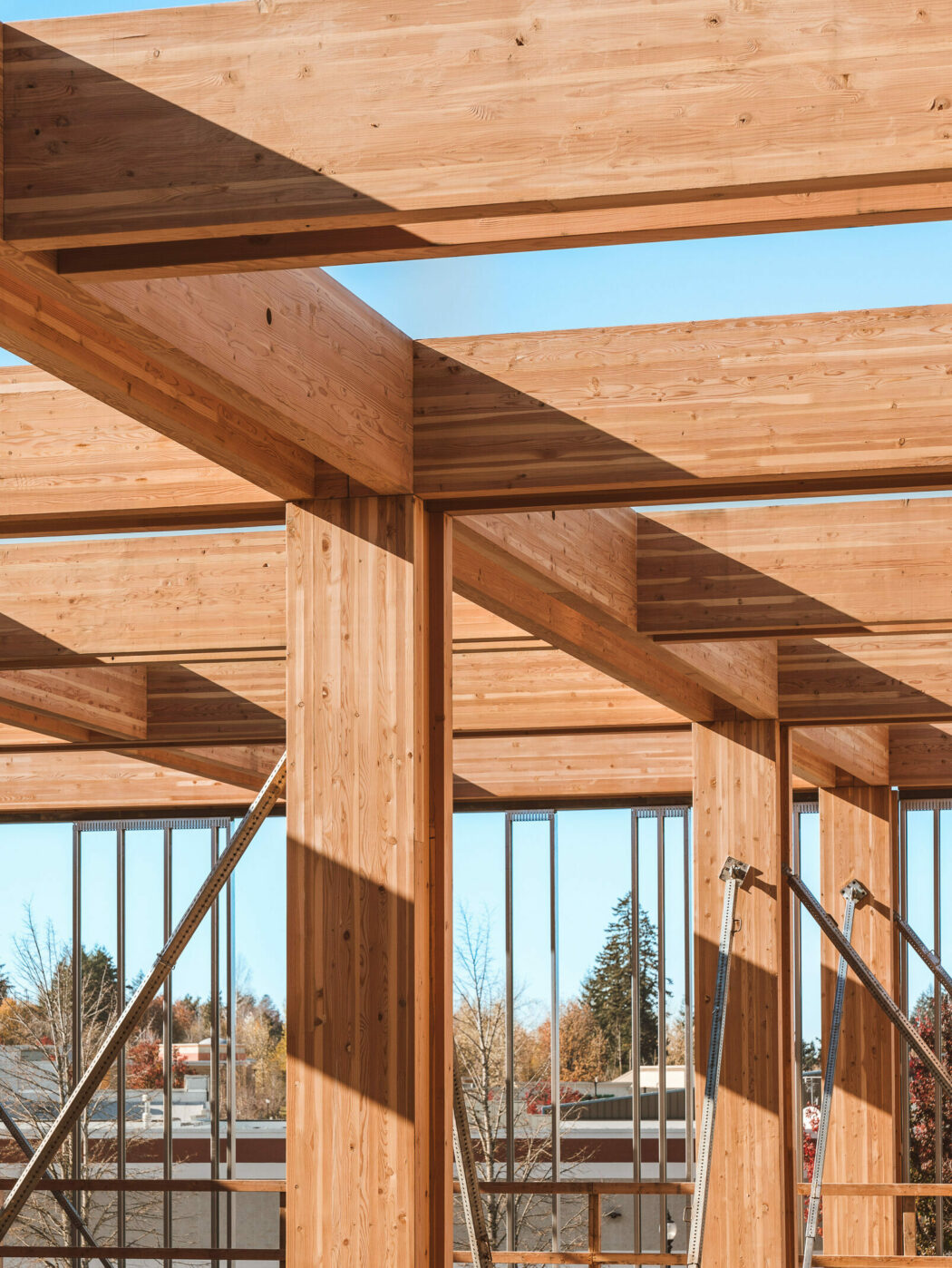
GLULAM BEAMS + COLUMNS
Timberlab currently provides some of the highest quality glulam manufacturing and fabrication services in the domestic U.S. construction market. With facilities based in the heart of Oregon's timber basket, our operations ensure that your projects use the highest-grade lumber in the country. With extensive roots as a builder, we turned to glulam production in 2021 to meet the industry's growing need for large-scale custom fabrication, allowing the market to take on bigger and taller mass timber structures. In 2024, our team launched manufacturing operations with ambitions to grow the market supply and supporting regional timber economies. Offering multiple species types, we produce glulam that meets the most stringent performance aesthetic standards—making them ideal for a wide range of structural and architectural applications.
For more information about purchasing glulam, please contact us.
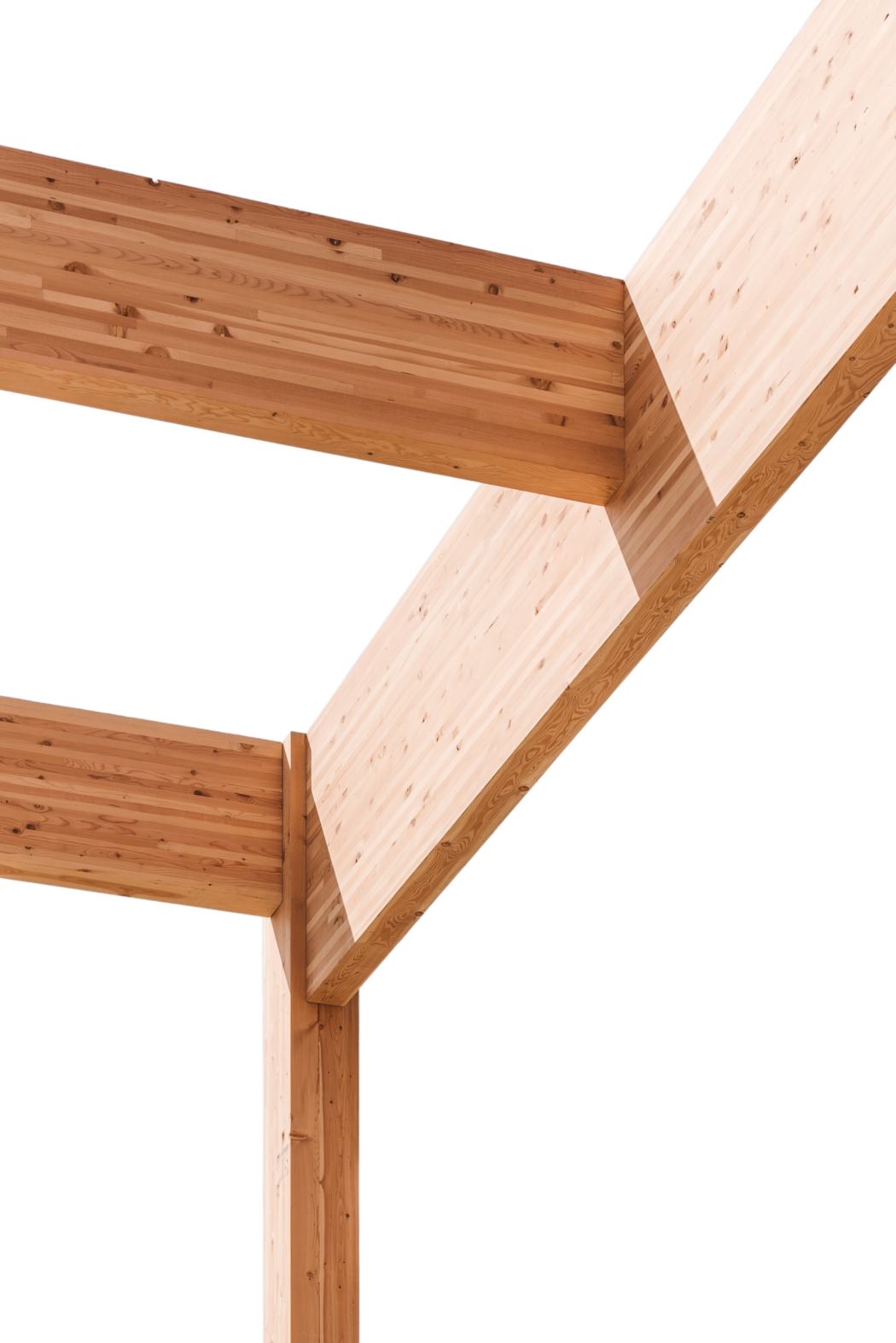
GLULAM STANDARD SIZES
Timberlab produces glulam in the following standard cross-section sizes. These sizes conform to standard sizes in the NDS up to 16 inches nominal width using either single or multiple-piece laminations (split laminations), as noted in the table below. The split lamination widths are based on the total laminating lumber widths in a layer minus an allowance to account for planning each side face after pressing to the finished width.
Timberlab can manufacture glulam up to 30 inches wide. Please contact us for member sizes wider than 24 inches.
Nominal Width | Douglas Fir | Alaskan Cedar | Southern Pine |
4" | 3 ⅛ | 3 ⅛ | 3 ⅛ |
6" | 5 ⅛ | 5 ⅛ | 5 ⅛ |
8" | 6 ¾ | 6 ¾ | 6 ¾ |
10" | 8 ¾ | 8 ¾ | 8 ½ |
12" | 10 ¾ | 10 ¼ (SL) | 10 ½ |
14" | 12 ¼ (SL) | 12 ¼ (SL) | 12 (SL) |
16" | 14 ¼ (SL) | 14 ¼ (SL) | 14 (SL) |
— | 16 ¼ (SL) | 16 ¼ (SL) | 16 ¼ (SL) |
— | 18 ¼ (SL) | — | 18 ¼ (SL) |
— | 20 ¼ (SL) | — | 20 ¼ (SL) |
— | 22 ¼ (SL) | — | 22 ¼ (SL) |
— | 24 (SL) | — | 24 (SL) |
SL = Split Lamination |
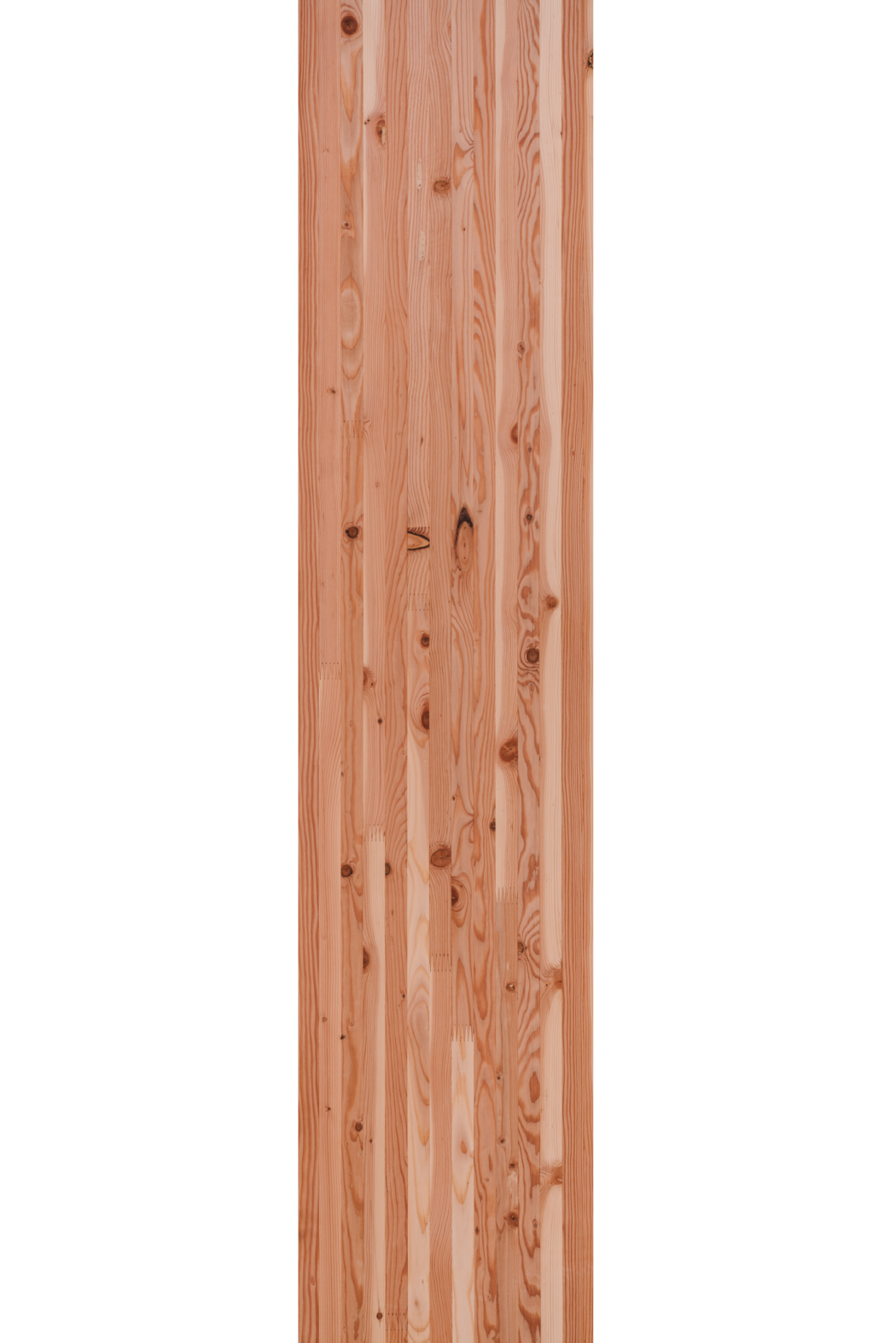
STANDARD DEPTHS
Standard depths are in multiples of the standard lamination thickness:
Douglas Fir: 1-1/2 inches
Alaskan Cedar: 1-1/2 inches
Southern Pine: 1-3/8 inches
Glulam depths can be a minimum of (2) laminations, although our standard depths start at a minimum of (4) laminations. Our maximum standard glulam depth is 72 inches. Please contact us for information about producing glulam up to a maximum depth of 118 inches.
Mass Timber Species Offerings

Bioregion: Central British Columbia south along Pacific Coast to central California, central Mexico, also Rocky Mountains to Arizona, Texas
Appearance: Sapwood is generally a light straw color. Heartwood is a deep russet brown. Grain is straight or slightly wavy.
Density: 32 - 35 lb/ft³ (at 15% moisture content)
510 - 560 kg/m³ (at 15% moisture content)
Notable Characteristics: Stiff and strong for its weight, among the most dense softwoods in North America. Dimensionally stable, glues well, and machines well.
Durability: Requires preservative treatment for wet service conditions. Pressure treatment options both with and without incising of the wood to achieve durability requirements are available.
Availability: Douglas-fir accounts for 37% of forest land in Oregon, with 10.9 million acres of cover. While Douglas fir populations are sensitive to increasing temperatures that produce drought events and higher pest infestations, it is the most prevalent tree species in the Pacific Northwest.
Notable Projects: Portland International Airport | Shevlin Crossing | Northlake Commons

Bioregion: Coastal regions of Alaska, British Columbia, and the Pacific Northwest of the United States
Appearance: Lightest in color, with straight grain. Sapwood is whitish-yellow and not distinct from Heartwood. When left exposed outdoors, weathers to a uniform gray.
Density: 26 - 31 lb/ft³ (at 15% moisture content)
420 - 500 kg/ m³ (at 15% moisture content)
Notable Characteristics: The heartwood is naturally durable due to natural extractives that also provide a pleasant aroma.
Durability: Naturally durable. Resistant to decay from water infiltration, insects, and fungi.
Common Applications: The heartwood can be used in exterior above ground applications that are exposed to wetting.

Bioregion: Southeastern United States
Appearance: Sapwood ranges from white to yellow or golden. Heartwood from yellow to reddish-brown. Distinct grain pattern.
Density: 33 - 39 lb/ft³ (at 15% moisture content)
530 - 625 kg/ m³ (at 15% moisture content)
Notable Characteristics: Highest specific gravity of all common softwoods.
Durability: Requires preservative treatment for wet service conditions. Pressure treatment options to achieve durability requirements are available.
Availability: Widely available, Southern Pine forests are some of the most productive in the world. Grown in a vast band in the southern United States, near sawmills.
Notable Projects: Tom Lee Park | Live Oak Bank

Spruce Pine Fir (SPF)
Hemlock Fir
European Spruce