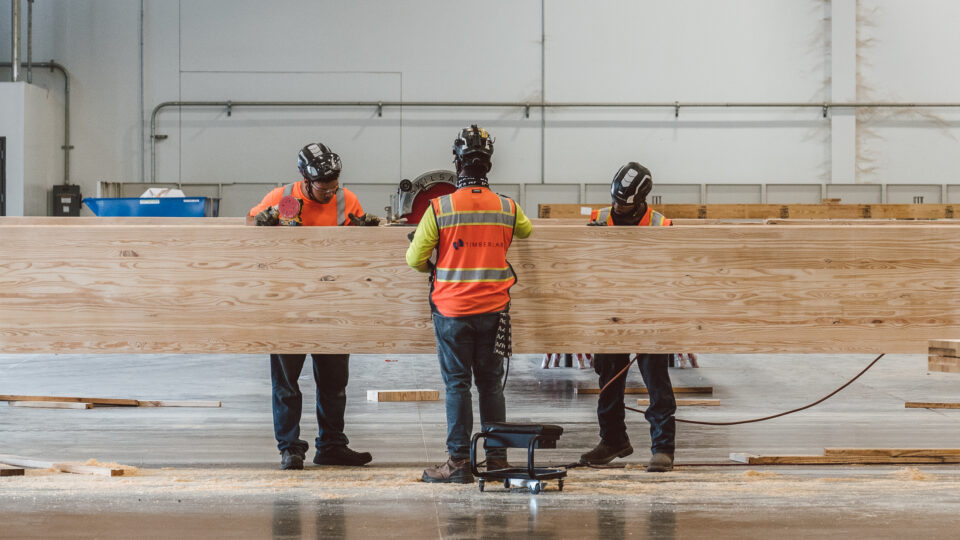
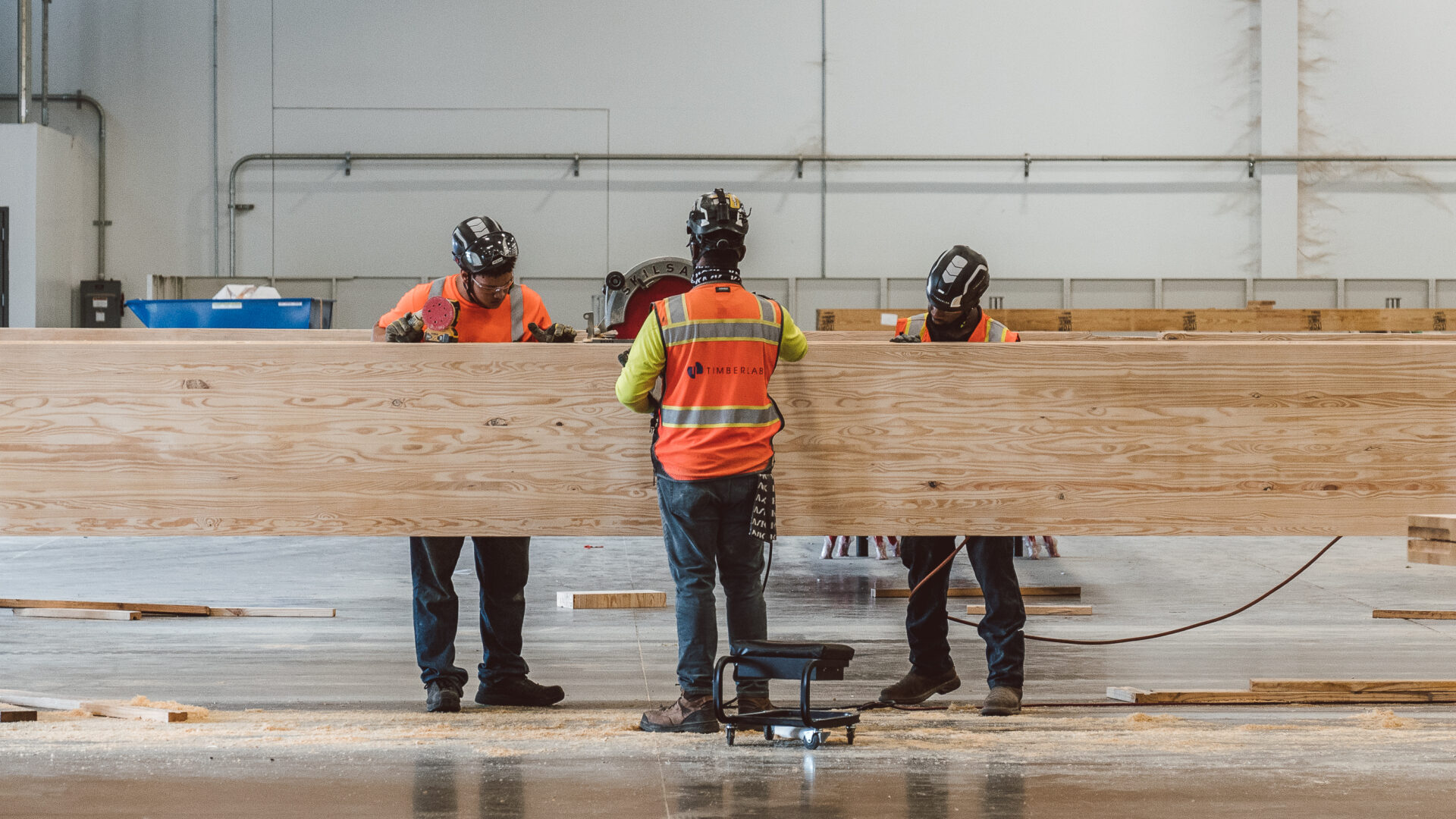
Author: James Alexander
Publication: Timberlab
03.27.23
Timberlab Opens New East Coast Fabrication Facility
THE SOUTHEAST GAINS INNOVATIVE MASS TIMBER ENGINEERING AND FABRICATION FACILITY IN GREENVILLE, SOUTH CAROLINA
(Greenville, SC) Timberlab, a nationwide provider of holistic mass timber systems, is opening its second glued laminated timber (glulam) fabrication facility in Greenville, SC. Timberlab's goal is to provide the Eastern United States with a more regional platform for a sustainable, low-carbon building material and accelerate the mainstream adoption of mass timber construction to benefit the planet and its people.
The newly renovated 75,000-square-foot East Coast facility begins operations in April and expects to be at full capacity by the second quarter of 2024. Staffed by 30 manufacturing and timber professionals, the Timberlab facility is the largest of its kind planned in the region, increasing the regional capacity of the fabrication of large glulam members for mass timber structures. The facility is equipped with state-of-the-art CNC machines and can produce timber to build an estimated one million square feet annually once at full capacity. Currently, there are only three facilities east of the Mississippi River capable of fabricating engineered wood products.
“Greenville was selected due to its close proximity to an abundance of southern yellow pine that is durable, renewable, and fast-growing and – mainly because of that – has emerged as the species of choice for producers east of the Mississippi River,” says Manufacturing Director Jared Revay. “There are a significant number of glulam producers throughout the Southeast who need a value-add partner, like Timberlab, in order to fully participate in the commercial, prefabricated mass timber industry. As we saw in the Pacific Northwest, our Eastern US manufacturing center is expected to positively impact the Southeast with an expanded supply chain.”
In the past five years, the number of projects incorporating mass timber has doubled every two years, and this trend is expected to continue for the next 15 years. Timberlab expects the adoption rate in key areas along the Eastern seaboard to outpace this projection. Glulam columns and beams for the University of Arkansas’ Institute for Integrative and Innovative (I3R) building in Fayetteville, Ark., will be the first components fabricated in the East Coast facility.
"There is an existing network of timber suppliers and glulam manufacturers in the Southeast that have been operating for decades with limited opportunities to deploy their product," says Timberlab President Chris Evans. Glulam is a building product industrially manufactured from raw timber and designed for load-bearing structures. Timberlab procures glulam billets from regional glulam manufacturers and transforms billets into custom building components that are then assembled at the construction site. “The CNC fabrication is currently the significant pinch point in the mass timber supply chain and where Timberlab will make a tremendous impact not only for suppliers but also in the adoption of this sustainable building system.”
Timberlab is no stranger to the rapid upstart of new fabrication facilities and the demands of the mass timber industry. In 2020 it opened its first location in Portland, Oregon, where it produces timber annually to build an estimated 800,000 sq. ft. of fabricated glulam components for projects throughout the United States. By replicating its successful West Coast business model, the East Coast facility will support the Southeast’s trajectory as a new regional powerhouse for mass timber construction. "Our intention is to expand the supply chain and, thereby, reduce the cost of mass timber structures, ultimately promoting the deployment of timber for commercial buildings along the Eastern seaboard, particularly in the office, multifamily, civic, and higher education sectors,” says Evans.
“Our clients are drawn to the natural warmth of timber that improves both work and living environments and reduces the carbon footprint of the building by utilizing local and renewable materials,” adds Evans. Currently, Timberlab is delivering several precedent-setting, timber-driven commercial and civic projects throughout the Southeast. For Tom Lee Park in Memphis, Tenn., Timberlab recently installed a 17,000-sq. ft. exposed timber canopy with a complex, diagonal framework design. Also, construction is currently underway for Building Four of the Live Oak Bank campus, a 67,000-sq. ft. office building in Wilmington, N.C.
“We’re not only focused on the mass timber builds of today but also the implications and explorations of those of tomorrow,” continues Evans. In addition to its custom fabrication services, Timberlab also dedicates a team to pursue mass timber innovation and research. The firm partners with Clemson University and other universities across the United States, as well as the U.S. Forest Service, to advance the adoption of mass timber construction. Areas of focus have included fire testing, vibration testing, and seismic load testing for tall timber buildings.
Timberlab expects to tap local trade schools, community colleges, and universities to fulfill job opportunities, offering new career paths in engineering and fabrication. The company will employ up to 30 prefabrication and shop technicians, CNC machinists and programmers, and operations positions. In addition to engineers and fabricators, Timberlab’s robust construction crews travel nationally to install the firm’s mass timber structures. "A key to our success in this industry is that our team is vertically integrated," says Revay.
Timberlab evolved from Swinerton, a leading general contractor with offices across the country and early adopters and innovators of mass timber construction. Revay continues, “Because of our roots, we approach each project with a mindset of a general contractor and a focus on client and overall project success always in mind. When others say, ‘this won't work’ or ‘it has never been done before,’ Timberlab demonstrates the possibilities."
Media Contacts:
James Alexander
james.alexander@timberlab.com
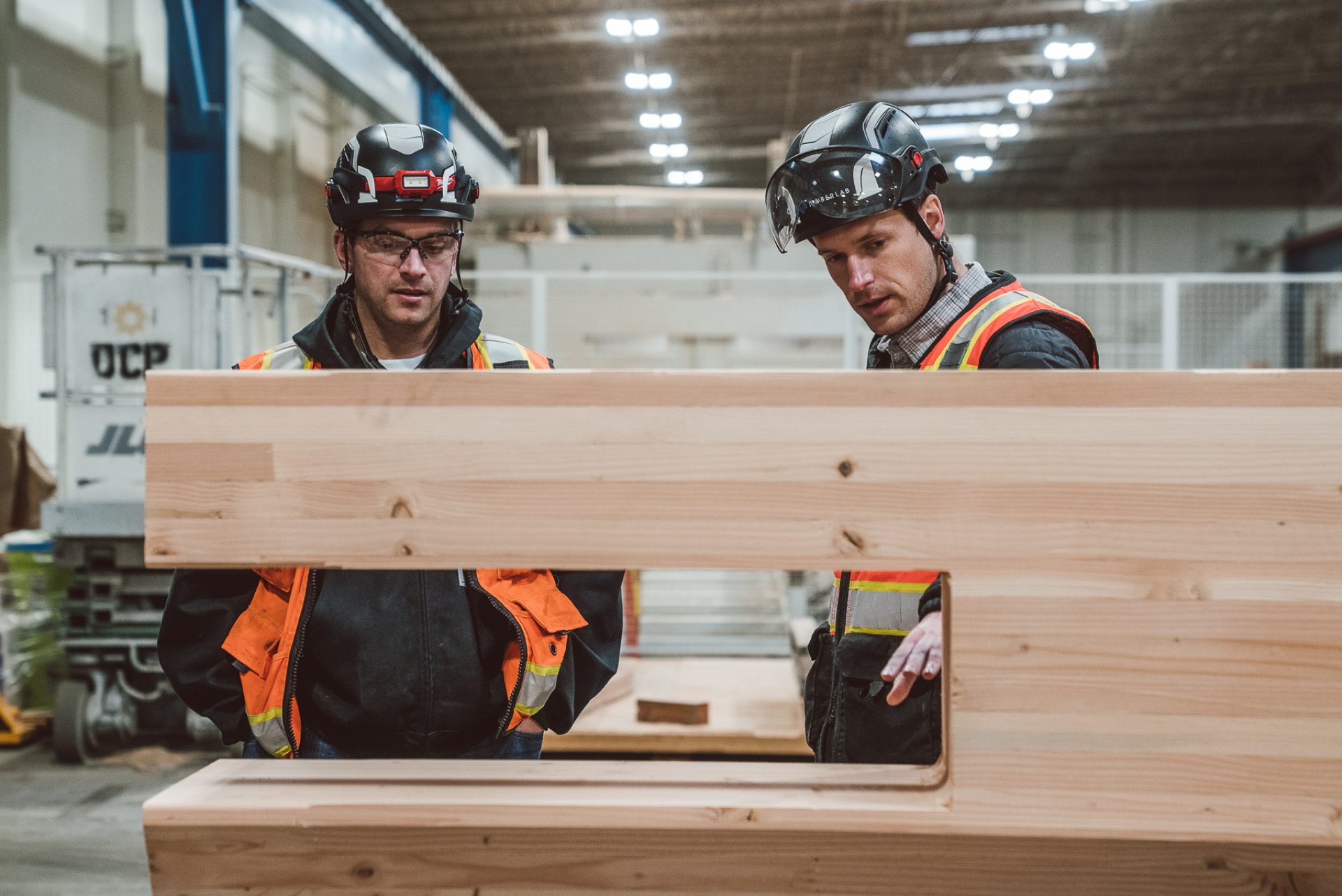
Insights, information, and inspiration.
Subscribe to our newsletter to stay up to date on the latest in mass timber.
Subscribe