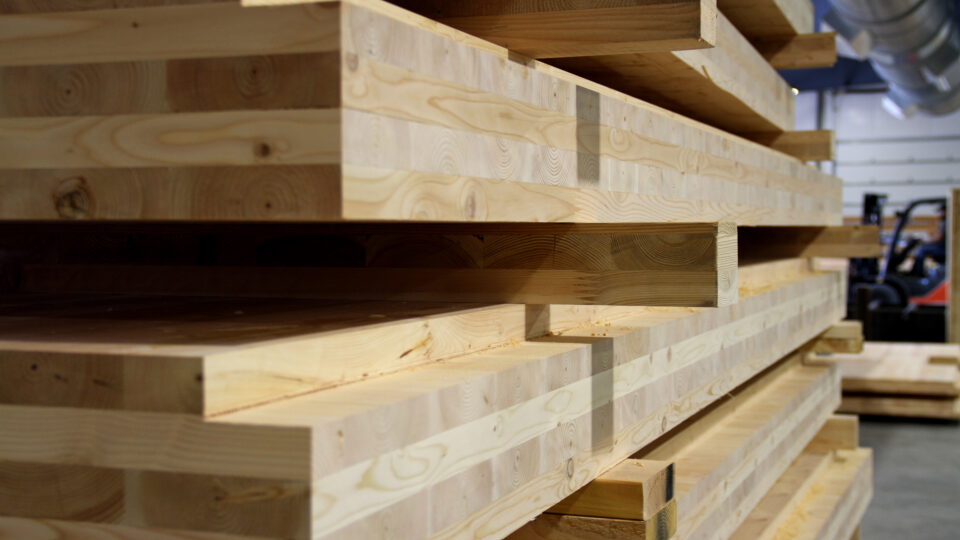
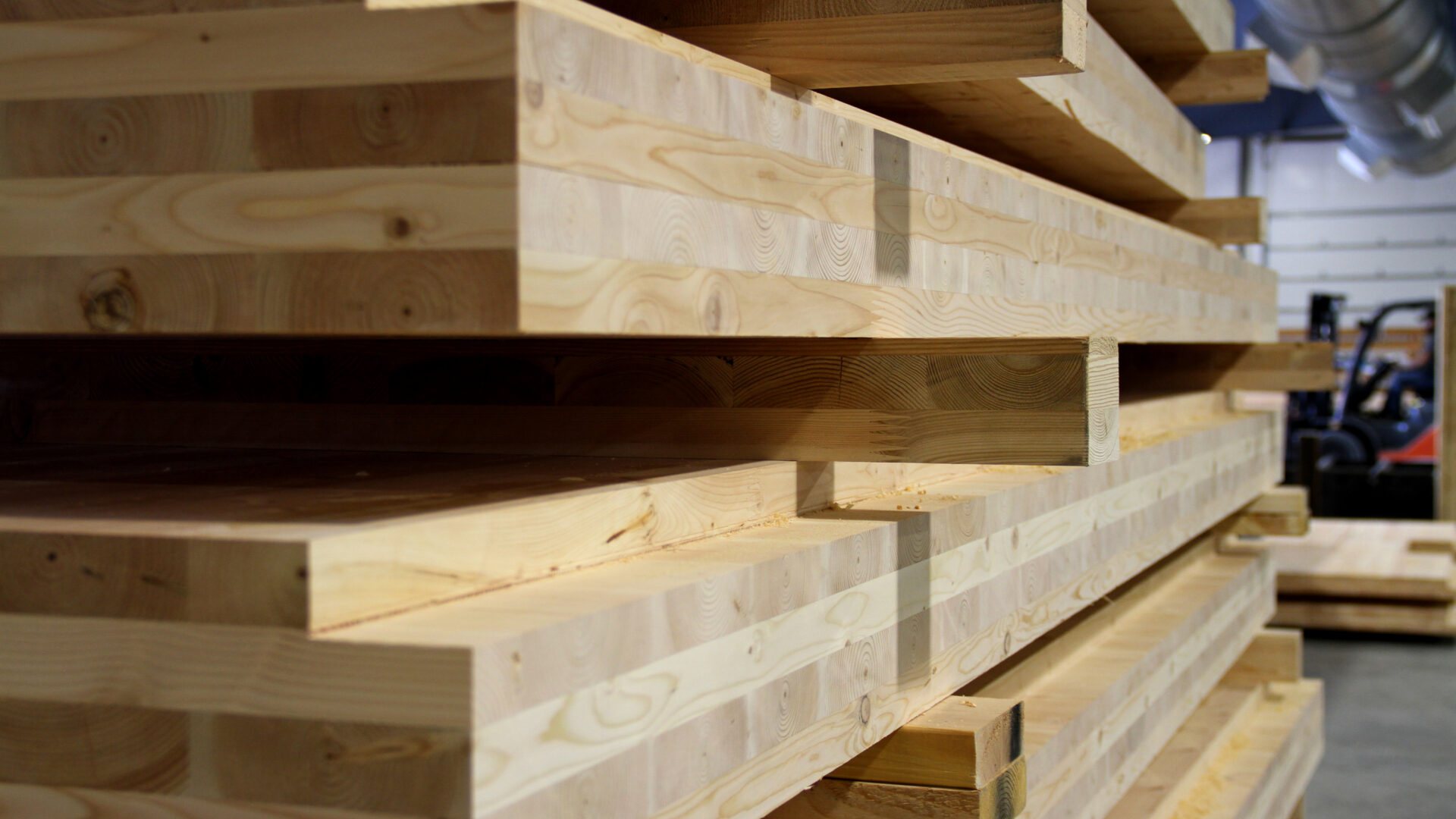
Author: James Alexander
Publication: Timberlab
11.15.24
A First Look into Timberlab's New Cross-laminated Timber Facility
Oregon's New Frontier in Cross-laminated Timber (CLT)
Timberlab is excited to announce its partnership with Kallesoe Machinery, a renowned leader and innovator in engineered wood manufacturing, as the selected machinery provider for our new CLT production facility in Millersburg, Oregon. This partnership ensures that our manufacturing is powered by the most advanced technology available, setting the stage for delivering superior quality panels.
This state-of-the-art facility, part of an investment from Timberlab’s parent company, Swinerton Incorporated, reflects our team’s dedication to advancing the mainstream adoption of mass timber in the U.S. construction market. Once completed, the 186,000-square-foot plant will produce an annual output of 100,000 cubic meters of CLT, making it one of the largest facilities of its kind in the nation. This initiative aligns with Timberlab's mission to streamline the mass timber supply chain, ensuring affordability, high quality, and wide usability of timber in construction projects.
The facility is strategically located in Oregon’s mid-Willamette Valley, a hub for mass timber innovation and home to leading academic research programs such as Oregon State University and the TallWood Design Institute. Timberlab's proximity to these institutions will foster collaboration and innovation, solidifying the Pacific Northwest’s reputation as a leader in sustainable construction materials. The facility will also bring economic benefits to the region, creating 100 new manufacturing jobs and supporting the broader goals of the Mass Timber Tech Hub designation from the U.S. Department of Commerce.
The Technology: Kallesoe's State-of-the-Art CLT Line
At the heart of the new facility will be Kallesoe’s high-performance CLT press, a game-changer in precision, accuracy, and efficiency. What sets Kallesoe's apart is its innovative radio frequency (RF) curing, which has been proven to reduce press times while ensuring uniform glue curing across all layers of the CLT panel. The outcome? Stronger, more durable panels built to excel in any application.
Another significant advantage of the line is its flexibility. Panels can reach lengths of up to 60 feet and widths of 11.5 feet, accommodating the needs of a diverse array of project types.
How It Works: From Lay-Up to Press
The process of creating cross-laminated timber (CLT) panels begins with Timberlab sourcing some of the highest-quality Douglas fir lamstock, grown in the Pacific Northwest's timber basket. This region is renowned for producing strong, straight-grained lumber that is ideal for mass timber applications. The lamstock is meticulously prepared for layering, with each piece planed to exact dimensions to ensure optimal adhesion and alignment during assembly.
Once the lamstock is layered, alternating grain directions in each layer provide the strength and stability CLT panels are known for. Hydraulic presses, powered by Kallesoe’s advanced technology, play a critical role in this process. Hydraulic presses apply a uniform, multi-directional pressure across the panel, compressing the layers while the adhesive cures. This system ensures a dense and durable bond between layers, resulting in panels that meet and exceed rigorous structural standards.
Why Kallesoe?
Kallesoe’s machinery is renowned for its adaptability, offering tailored solutions to meet the unique needs of each manufacturer. With decades of expertise, its systems are designed for scalability and high throughput, producing up to 80 cubic meters of CLT in a standard shift. The radio-frequency technology and robust design also minimize downtime and maintenance requirements, making it an ideal choice for Timberlab's high-performance manufacturing goals.
The Future of CLT with Timberlab
Timberlab’s new CLT facility represents a significant step forward in the company’s commitment to vertical integration, positioning Timberlab as a comprehensive partner for all mass timber needs. By seamlessly incorporating the Millersburg CLT plant into Timberlab’s existing suite of services—spanning design, engineering, fabrication, and installation—projects will benefit from a streamlined supply chain. This integration ensures lower production costs, greater quality control, and enhanced efficiency, all of which translate to value for our clients.
Timberlab’s recently acquired lumber mill in Philomath, Oregon, is a key element supporting the new CLT facility. This mill will provide a consistent supply of high-quality Douglas fir lamstock sourced from the immediate region. Timberlab can guarantee its products' strength, precision, and reliability by managing the production pipeline from raw material to finished CLT panels while minimizing waste and reducing lead times.
This approach allows Timberlab to deliver mass timber solutions tailored to the needs of each project, ensuring everything from material selection to installation is executed with excellence. With this fully integrated framework, Timberlab is not just a material supplier but a trusted partner, delivering sustainable, cost-effective, and innovative mass timber systems for projects across North America.
For more details about the Kallesoe CLT press and its integration at Timberlab’s Millersburg facility, please contact our team directly.
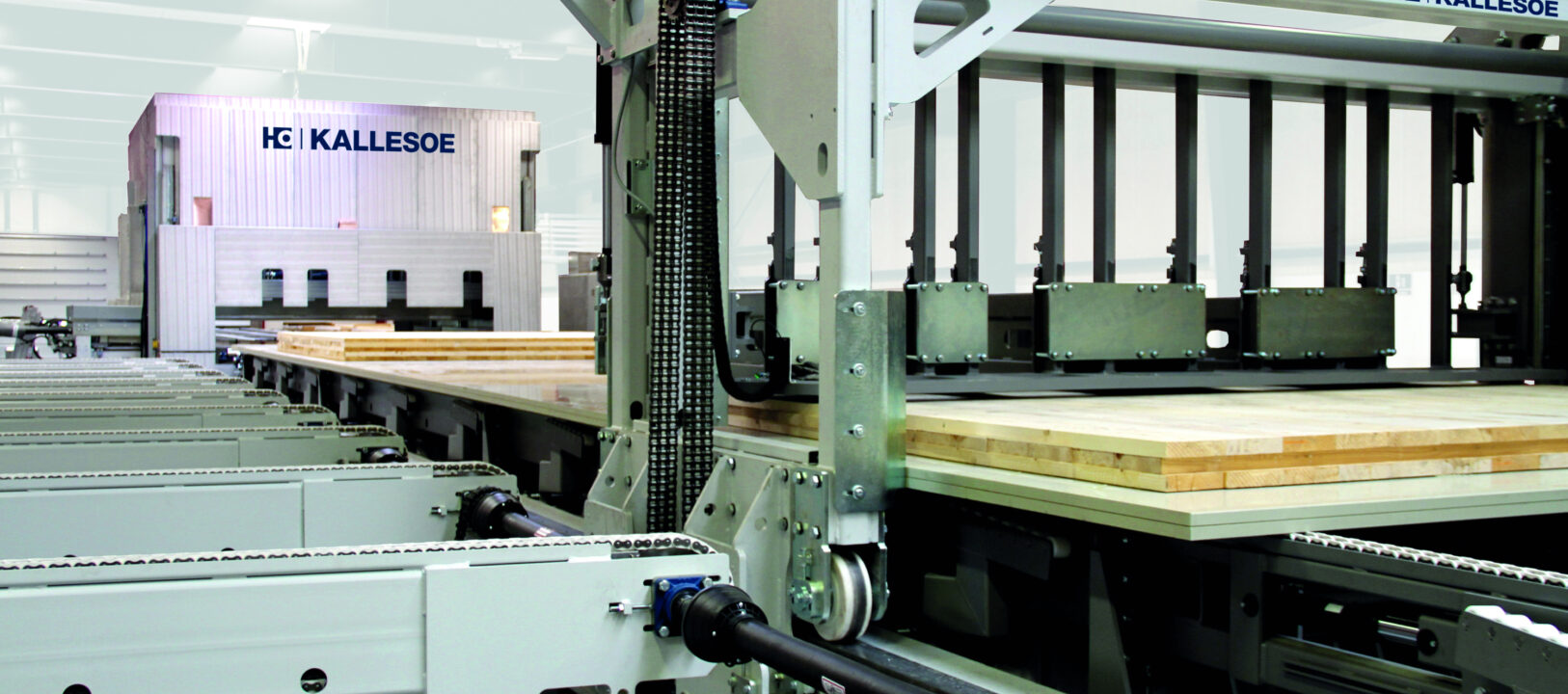
Related Articles
Insights, information, and inspiration.
Subscribe to our newsletter to stay up to date on the latest in mass timber.
Subscribe