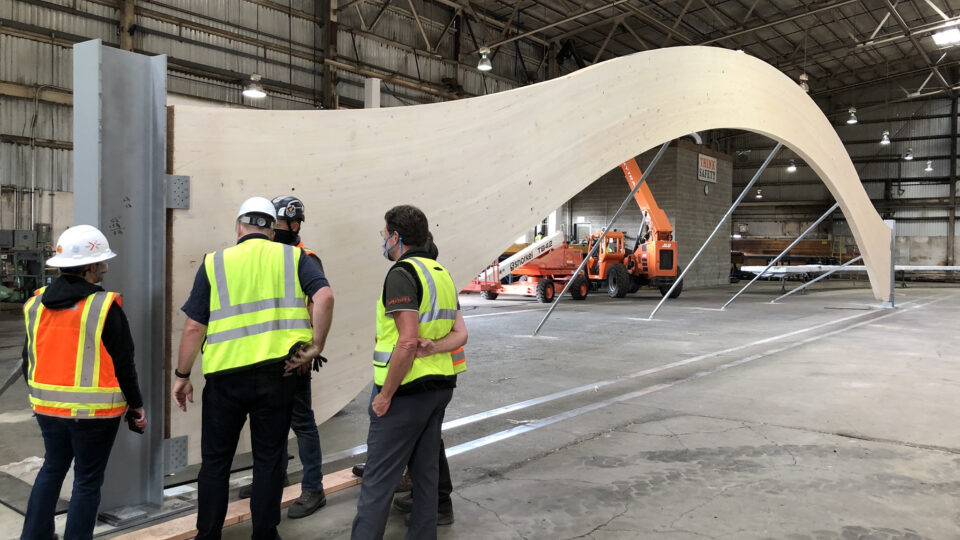
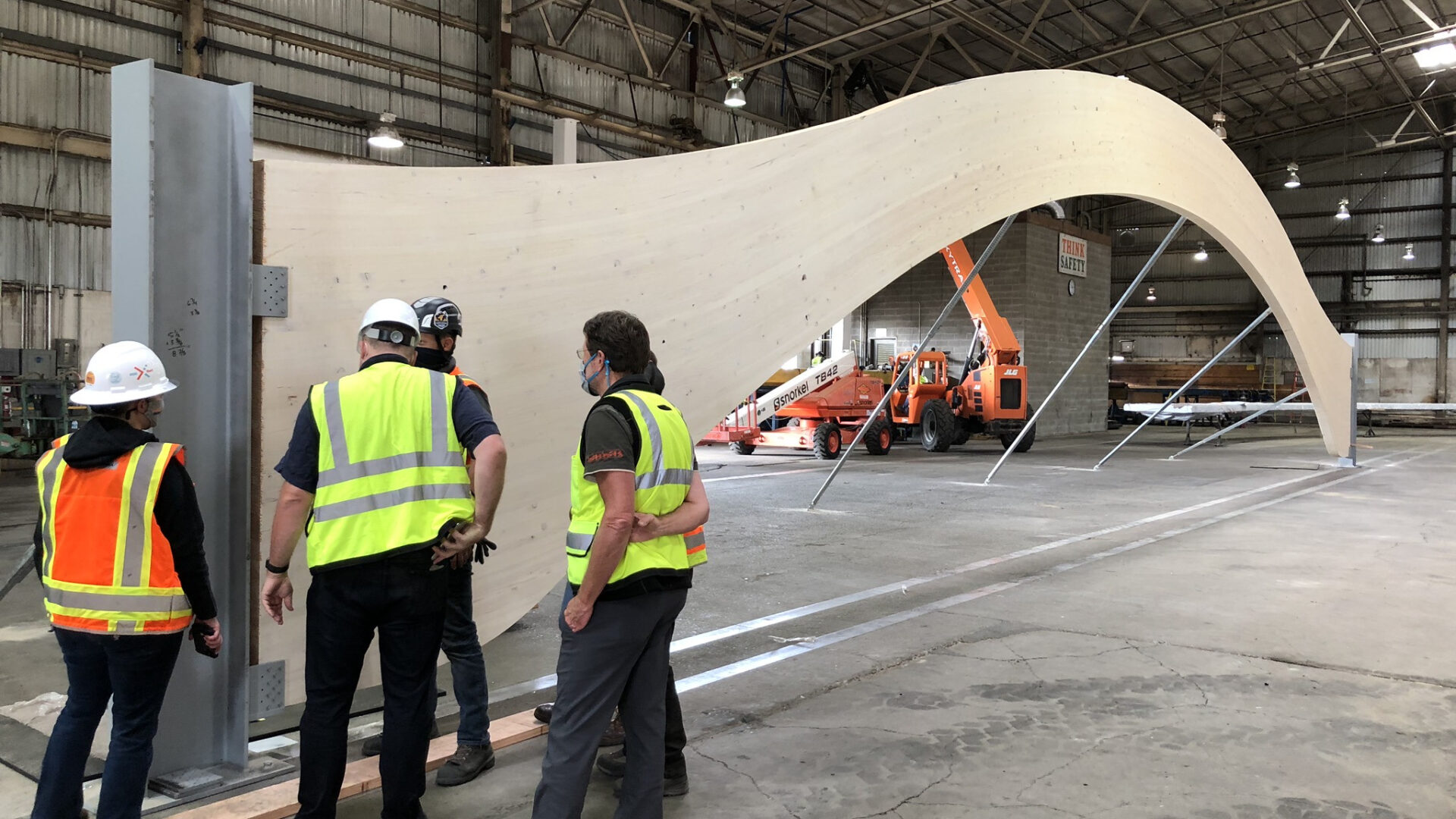
Author: Josh Kulla
Publication: Daily Journal of Commerce
08.16.21
Ingenious Solution: Prefabricating PDX Airport Timber Roof
Prefabrication solved a roof puzzle for the Portland International Airport main terminal project team.
But instead of a typical ground-up building process, construction of the most striking and eye-catching portion of that new structure – its roof – is taking place in the northeast corner of the airport property, next to the Port of Portland Fire Department headquarters.
Designed by ZGF Architects to emulate Oregon’s lush forestlands, the mass-timber roof is an ode to the local environment. The undulating structure consists of a skeleton of enormous steel girders fabricated by Evraz in Portland. Those are connected by a series of massive, arching glulam beams made from Douglas fir by Zip-O-Log Mills of Eugene. Topping it off are hundreds of two-inch mass-plywood panels made by Freres Lumber of Lyons.
“It was very important to Port of Portland leadership, so they worked strategically with ZGF on developing the specifications on this prescribed sourcing,” said Katrina Day, a senior project manager with Hoffman Skanska Joint Venture, the project’s general contractor. “It’s intended as a nod to the local community and making sure that we’re reinvesting in Oregon for the project.”
The prefabricated roof is an ingenious solution to some unique construction problems.
First is the building site: a busy international airport that before the pandemic was serving nearly 20 million travelers per year. The sheer volume of people moving though PDX and the importance of the airport as a travel hub means it cannot be shut down for construction – and assembling the roof in place would have required that for safety and security reasons.
“If you stick-built this over the terminal, these members are too big,” Hoffman Skanska senior superintendent Jason Koski said. “You couldn’t build anything like this and have an occupied building. So, by doing these large modules, we’re able to keep the terminal open at all times during construction.”
Instead, the project team took over a 20-acre site next to the near the fire department headquarters and poured a reinforced concrete pad engineered to support the weight of not only the roof structure, but also the massive hydraulic jacks and self-propelled modular transporters that will be used to move the finished roof segments across the airport’s north runway to their eventual home.
“We’ll set those at night in roughly a six-hour window where we can shut the building down,” Koski said.
The full roof will be assembled in spring 2022 from 20 separate pieces. Of those, 16 will be “super modules” featuring arched glulam beams topped with mass-plywood panels fabricated by Freres Lumber and milled into shape by Swinerton subsidiary Timberlab at its Northeast Portland plant. The other four will be smaller “cassettes” to fill in spaces left over.
“Nobody has ever made them to this standard, and nobody has ever made an arched glulam this large,” Day said. “In fact, in the design, they were spliced halfway through because there was no standard for designing to know whether they were constructable. So, Zip-O (employees) took it upon themselves to build a full-size mockup to ensure we could eliminate the splice.”
That effort was successful, and the resulting 80-foot-long beams are up to 9 feet tall.
The wood for the glulams was sourced from local forestlands managed by the Yakama, Coquille and Skokomish tribes as well as other landowners practicing responsible forest management.
“We’re putting our first layer of roofing on,” Koski said. “And we’re putting in all the lighting conduit, the fire alarm conduit, the sprinkler system, the roof drains, and then acoustical panels.”
About 60 percent of the lattice that decorates the interior part of the structure in graceful curves will be installed beforehand, according to Swinerton superintendent Brendan Kelly.
A lot of work was needed in the design and engineering phase to come up with the plan, Port of Portland Construction Services Manager Brad Harrison added.
“We started from scratch, but to stick-build this thing it became apparent that it would almost shut down the airport,” he said. “The contractor was like, the more modular construction you can do, the better, from a whole cost perspective and a safety perspective.”
Insights, information, and inspiration.
Subscribe to our newsletter to stay up to date on the latest in mass timber.
Subscribe