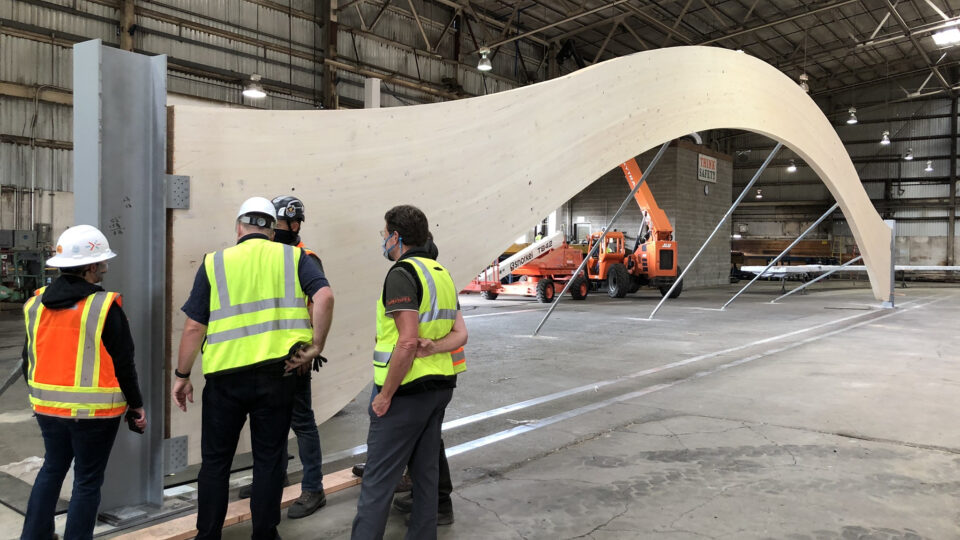
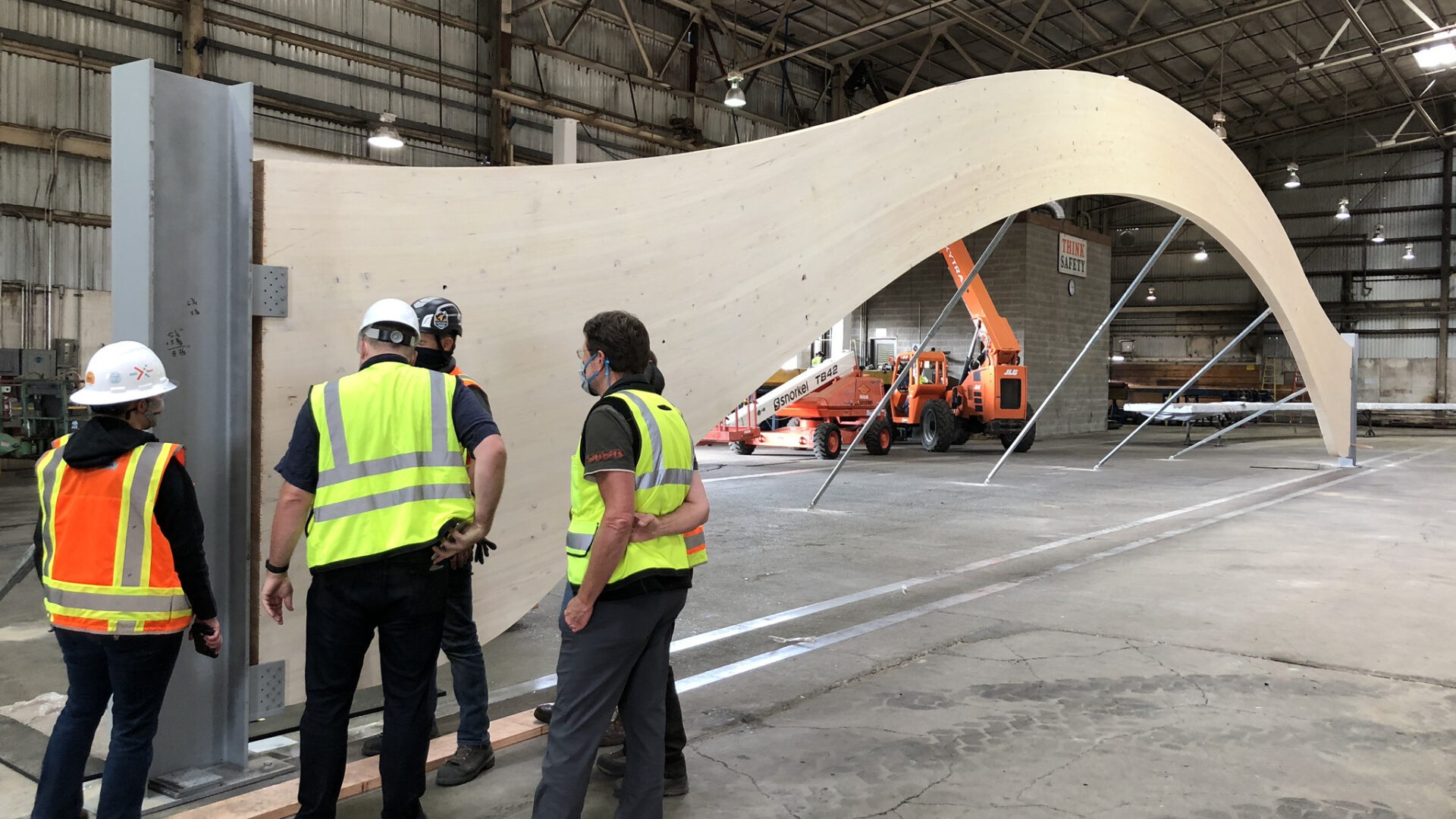
Author: CadMakers
Publication: Cadmakers.com
05.05.22
Fabrication/Construction Process of the Highly Complex Mass Timber Roof
Portland International Airport (PDX) is getting a $2-billion makeover and the innovative, nine-acre, seismically isolated curved mass timber roof of the main terminal is at the epicenter of it all. The roof on the terminal core (TCORE) of PDX is part of a revamp to give it a warmer and people-friendly atmosphere. It consists of 277 80-ft glulam beams with 7.5 ft depth and a 16-ft arch. They are supported by large steel girders, between each of which, is an interface with the glulam at the bucket connections. The deck on top is made of 1347 2-inch thick locally sourced mass plywood panels (MPP) creating a diaphragm on the roof allowing for 10–ft on center beam spacing. The roof is a giant sloping arch with large skylights and an undulating edge. There are more than 30,000 individual sticks of 3x6 lattice on the underside of the glulam beams. This project required a large team comprised of multiple companies/experts working together towards the same goal. Coordination and teamwork have been key to the success of the overall project. World-class contractor - Swinerton and its Mass Timber-focused affiliate Timberlab, are handling the full timber fabrication & installation scope for this project with help from CadMakers (a Vancouver, Canada-based VDC consultancy) providing digital fabrication twin services.
Mass timber uses state-of-the-art technology to glue, nail, or dowel wood products together in layers. The results are large structural panels, posts, and beams. BIM/VDC, which is traditional 3D computer modeling used for coordination, has been pushed to new levels on this project by involving general contractors, superintendents, project engineers, and project managers to develop a fabrication level digital twin to assist the design, fabrication and installation process. The power of automation allows us to generate thousands and thousands of pieces with complex geometry within a strict project timeline.
In addition, to keep the airport in operation, the roof had to be split into 15 modules, pre-installed at a lay-down yard, and reassembled at the terminal within a limited time window (airport shutdown hours). Therefore, extensive Design for Manufacture and Assembly (DFMA) considerations have been applied to the project and multiple dynamic installation processes have been simulated from the digital twin in advance.
CadMakers uses 3DExperience/CATIA, the same software being used by major aerospace and automotive companies, to create the fabrication package and installation guides for the project. One fun fact here is this might be the 1st time the aircrafts and the airport come from the same design platform in the manufacturing and construction world.
Insights, information, and inspiration.
Subscribe to our newsletter to stay up to date on the latest in mass timber.
Subscribe